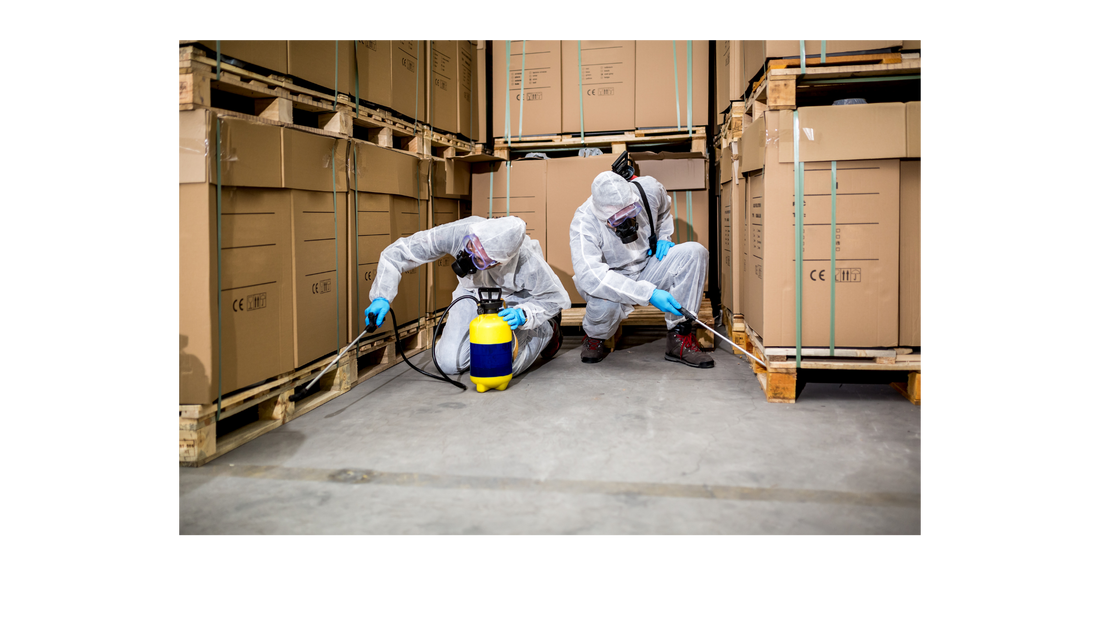
What is Industrial Hygiene?
Share
Industrial hygiene (also known as occupational hygiene) is the science of anticipating, recognizing, evaluating, and controlling workplace conditions that may cause illness, injury, or discomfort. It involves:
- Identifying Hazards: Recognizing potential risks like chemicals, noise, or ergonomic stressors.
- Evaluating Risks: Measuring exposure levels and assessing their impact on health.
- Controlling Hazards: Implementing measures to reduce or eliminate risks.
Industrial hygiene is not just about compliance—it’s about proactively protecting workers and improving their quality of life.
Why is Industrial Hygiene Important?
- Protects Worker Health: Reduces the risk of occupational illnesses like respiratory diseases, hearing loss, or skin conditions.
- Boosts Productivity: Healthier workers are more productive and engaged.
- Ensures Compliance: Helps businesses meet safety regulations and avoid fines.
- Saves Costs: Prevents costly medical expenses, workers’ compensation claims, and downtime.
Common Workplace Hazards Addressed by Industrial Hygiene
- Chemical Hazards: Exposure to toxic substances like solvents, gases, or dust.
- Example: Workers in a paint factory may be exposed to harmful fumes.
- Physical Hazards: Noise, radiation, extreme temperatures, or vibration.
- Example: Construction workers exposed to loud machinery without hearing protection.
- Biological Hazards: Bacteria, viruses, or mold.
- Example: Healthcare workers at risk of exposure to infectious diseases.
- Ergonomic Hazards: Poor workstation design or repetitive motions.
- Example: Office workers developing carpal tunnel syndrome from improper keyboard use.
The Industrial Hygiene Process
- Anticipate Hazards: Identify potential risks before they become problems.
- Example: Assessing the risks of a new chemical before introducing it to the workplace.
- Recognize Hazards: Observe and document existing risks.
- Example: Noticing high noise levels in a manufacturing plant.
- Evaluate Hazards: Measure exposure levels and compare them to safety standards.
- Example: Using air sampling to test for chemical concentrations.
- Control Hazards: Implement measures to reduce or eliminate risks.
- Example: Installing ventilation systems to remove harmful fumes.
Safety Standards Related to Industrial Hygiene
Several safety standards emphasize the importance of industrial hygiene:
- OSHA’s Permissible Exposure Limits (PELs)
- Sets legal limits for worker exposure to hazardous substances.
- Example: OSHA’s PEL for benzene is 1 part per million (ppm) over an 8-hour workday.
- ACGIH Threshold Limit Values (TLVs)
- Provides guidelines for safe exposure levels to chemicals and physical agents.
- Example: ACGIH recommends a TLV of 85 decibels for noise exposure over an 8-hour day.
- ISO 45001:2018 - Occupational Health and Safety Management Systems
- Provides a framework for managing workplace health and safety risks, including industrial hygiene.
- NIOSH Recommendations
- The National Institute for Occupational Safety and Health (NIOSH) offers research-based guidelines for controlling workplace hazards.
Best Practices for Implementing Industrial Hygiene
- Conduct Regular Risk Assessments: Identify and evaluate hazards in your workplace.
- Monitor Exposure Levels: Use tools like air sampling, noise dosimeters, or heat stress monitors.
- Implement Engineering Controls: Use ventilation systems, noise barriers, or automated equipment to reduce risks.
- Provide PPE: Equip workers with gloves, masks, earplugs, or other protective gear.
- Train Employees: Educate workers on hazard recognition and safe work practices.
- Review and Improve: Continuously update your industrial hygiene program based on new risks or regulations.
Real-World Example: Industrial Hygiene in Action
A chemical manufacturing plant noticed that workers were experiencing headaches and dizziness. An industrial hygienist conducted air sampling and found high levels of toluene, a toxic solvent. To address the issue, the company:
- Installed local exhaust ventilation to remove fumes.
- Provided respirators to workers.
- Conducted regular air monitoring to ensure compliance with OSHA’s PELs.
As a result, worker symptoms decreased, and the company avoided potential fines.
Final Thoughts
Industrial hygiene is a cornerstone of workplace safety, protecting employees from environmental hazards. By anticipating, recognizing, evaluating, and controlling risks, businesses can create healthier, safer, and more productive workplaces.